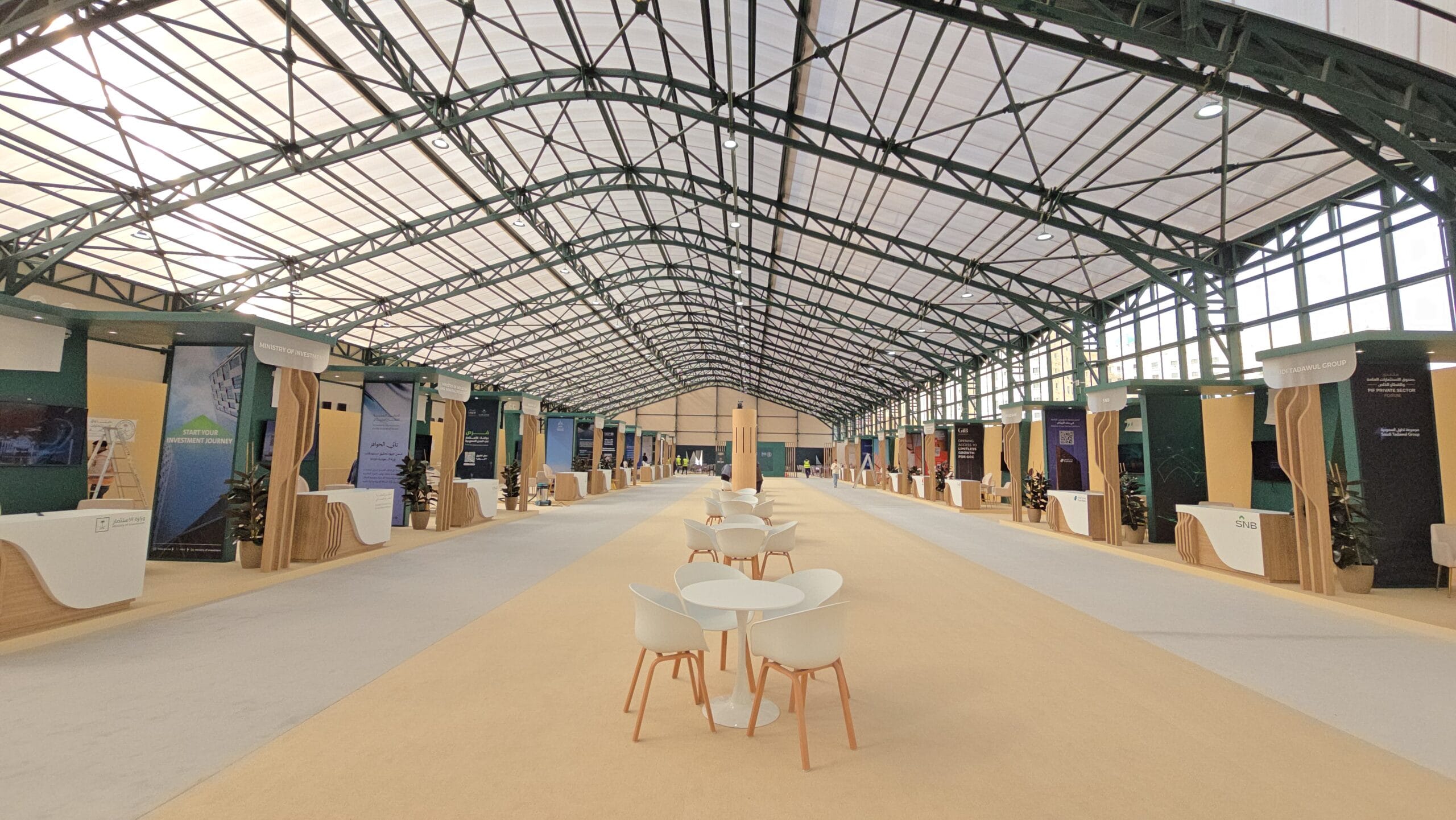
Introduction
Natural daylight is a crucial element in commercial and industrial building design. Adequate daylight improves occupant well-being, productivity, and even safety. In large facilities like warehouses, factories, malls, or airports, achieving the optimal light transmission inside can be challenging. This is where modern skylight systems, especially those made from polycarbonate and fiberglass-reinforced polyester (GRP), play a vital role. These translucent roof panels can flood interior spaces with natural light, helping meet recommended illumination levels (measured in lux) for various activities while reducing the need for artificial lighting. In this article, we explore how polycarbonate and GRP skylights contribute to optimal daylighting, the typical lux requirements across different building types, and the technical distinctions between these materials. DOMER’s line of skylight solutions (and its sub-brands) will be highlighted as prime examples of commercial skylight systems that deliver energy-efficient industrial daylighting solutions.
Importance of Daylight and Lux Levels in Large Buildings
“Lux” is the unit of illumination, indicating how much light is present in a given area. Different environments and tasks require different lux levels for comfort and efficiency. For instance, an open office might need around 500 lux for comfortable reading and computer work, whereas a storage warehouse can function with around 150 lux in aisles. Providing sufficient light is not just a code requirement, it directly impacts worker productivity, accuracy, and safety. Traditionally, this was achieved with electric lighting, but large commercial buildings can reduce energy costs significantly by harnessing daylight. Skylights and translucent roof panels allow natural light to penetrate deep into a building, maintaining those optimal lux levels during daylight hours. Modern skylight designs also diffuse sunlight to eliminate glare and hotspots, creating an evenly illuminated environment that enhances visual comfort. In essence, daylighting through skylights strikes a balance between meeting illumination standards and promoting energy efficiency by leveraging free natural light.
Lux Requirements by Building Type
Different building types have widely varying illumination needs. Below we outline typical recommended lux levels for several common commercial/industrial settings and explain how skylights help achieve these levels:
Warehouses and Logistic Centers
Skylights integrated into a warehouse roof provide abundant daylight, improving overall illumination in storage areas. Warehouses and logistic centers typically require relatively moderate light levels, but uniformity and coverage are important. Guidelines from lighting authorities (such as CIBSE and OSHA) often recommend a minimum of 150 lux at the floor level in general storage areas. In practice, warehouse aisles are commonly lit in the range of 100–200 lux for safe movement of personnel and forklifts. Critical task zones in warehouses, like packaging or inspection areas, may need stronger lighting (e.g. 200+ lux). Loading bays are brighter as well, often 300 lux or more, to ensure safety during loading/unloading of goods.
Skylights can effectively provide these illumination levels on clear days by channeling sunlight into the vast floor area. In high-bay warehouses with tall ceilings, continuous polycarbonate skylights or fiberglass skylight panels running along the roof can disperse daylight over large areas. Industry studies suggest that dedicating about 2–3% of the roof area to skylights in warehouses and distribution centers yields substantial daylight coverage. This percentage is usually enough to avoid dark spots while keeping lighting energy savings high. During sunny hours, a well-designed skylight layout can let warehouses operate under predominantly natural light, meeting the ~150 lux requirement and significantly cutting down on electrical lighting use. In large logistic parks (essentially expansive warehouses), DOMER’s standing-seam polycarbonate systems or long-span GRP panels can be installed in roof sections to uniformly illuminate aisles and storage racks. The diffused daylight from these systems ensures that even the depths of a storage area receive usable light, contributing to safer operations and energy efficiency.
Factories and Industrial Facilities
Industrial production facilities and factories demand higher lux levels than warehouses. Precise tasks like assembly, machining, or quality inspection require strong lighting for accuracy. General manufacturing or assembly areas often target around 500–750 lux of illumination. In detailed workstations (for example, electronics assembly or fine hand-crafting), recommended illumination can go up to 1000 lux or more. For instance, a standard factory workshop may be designed for roughly 750 lux ambient lighting, while a quality control station might have additional task lighting to reach 1000 lux on the work surface. These levels ensure that workers can see fine details and operate machinery safely.
In large factories, skylights are an excellent way to provide a base level of diffuse daylight across the facility. High-performance industrial skylight systems can deliver a broad spread of natural light, which can often achieve a few hundred lux on the factory floor under bright sky conditions. This significantly reduces the load on artificial lights during daytime. For example, translucent GRP panel skylights can be installed between opaque roof cladding to create well-lit production halls. Daylight alone might not always reach the full 500+ lux needed for detailed tasks (especially on overcast days), but it provides a substantial portion of it. The remaining illumination can be topped up by electric lighting as needed. The result is a hybrid lighting solution that is both energy-efficient and compliant with illumination standards. Additionally, natural light has been noted to improve worker morale in manufacturing settings, making spaces feel less cavernous and more welcoming. Many factories incorporate continuous ridge skylights or periodic dome skylights to maximize this benefit. With solutions like DOMER’s Vivid GRP skylight panels that offer high light transmission with diffuse distribution, industrial buildings can achieve bright, shadow-free environments ideal for precision work.
Offices and Workspaces
Office environments typically require bright, glare-free light for reading, computer use, and meetings. Standard recommendations for offices are on the order of 500 lux for general ambient lighting. At individual desks or workstations, 300–500 lux is considered a comfortable range for tasks like reading documents or keyboard work. Conference rooms and design studios might also aim for around 500 lux to keep occupants alert and focused. Insufficient lighting in offices can cause eye strain, while overly harsh lighting can lead to glare on screens; thus, quality of light is as important as quantity.
Skylights in office buildings are often used in top-floor open-plan offices, atriums, or large communal areas. While vertical windows are the primary daylight source in multi-story office buildings, single-story offices or the upper levels of buildings can greatly benefit from overhead skylights. Polycarbonate skylights or light wells can introduce soft, filtered daylight that complements window light. For instance, tubular skylights (such as DOMER’s Lumina series) can channel daylight from the roof down into an office interior, delivering natural illumination right above workstations. This can easily contribute a few hundred lux in the area directly beneath each skylight on a sunny day. One key advantage of skylights in offices is the diffused nature of the light (especially when using translucent or frosted materials), which minimizes glare on computer screens compared to direct sunlight from windows. Designs often include prismatic diffusers or frosted polycarbonate to scatter the incoming light. Office skylights are typically paired with automated lighting controls – sensors can dim or switch off electric lights when daylight is sufficient, ensuring the combined light stays around the recommended 500 lux level. The result is an energy-saving, comfortable lighting setup. Additionally, natural light has been shown to improve mood and cognitive function in workplaces, so incorporating skylights can have productivity benefits beyond just meeting a lux number.
Shopping Centers and Retail Areas
Retail environments like shopping centers, supermarkets, and showrooms generally require high illumination to create an inviting atmosphere and to clearly showcase merchandise. Common guidelines suggest about 500 lux for small retail shops and boutiques. Larger retail areas, such as malls or supermarkets, often use 750 lux as a target level, while hypermarkets or big-box stores might go up to 1000 lux in brightly lit sections. Display areas or shop windows can be even brighter (sometimes spotlighted to 1000+ lux) to draw attention to featured products. These high light levels help with visual merchandising and create a lively shopping experience.
Skylights play a prominent role in many modern shopping malls and large retail stores. It’s common to see extensive skylight strips or entire atrium roofs made of polycarbonate or glass in mall architecture. The reason is twofold: daylight enhances the aesthetic appeal of the space (making it feel more open and pleasant) and it provides a substantial amount of the required illumination for free. During daytime hours, a small atrium with a large skylight can often maintain general illumination in the hundreds of lux, greatly reducing how much electrical lighting is needed in those areas. According to industry recommendations, retail buildings benefit from a higher percentage of skylight coverage, roughly 5% of the roof area as transparent glazing, to achieve good daylight saturation. For example, in a large shopping center, a combination of overhead skylight panels and clerestory windows might be used to reach an average of 500–750 lux on the concourse floor in daytime. Supermarkets, which often have expansive flat roofs, can integrate rows of translucent roof panels or domed skylights across the ceiling to sprinkle daylight throughout the store. Customers not only get a better view of products under natural light (which has excellent color rendering), but the store also saves on energy. DOMER provides specialized translucent roofing systems for such applications, like vaulted polycarbonate skylights (e.g., ContiVault) that can cover large roof sections and bathe the retail floor in even, filtered daylight. These systems are designed with tints or coatings to prevent glare and overheating while still delivering the high lux levels retail spaces demand.
Airports and Transit Terminals
Airport terminals, train stations, and other transit hubs are expansive facilities that serve thousands of people daily. Proper lighting is critical for navigation, security, and comfort. Different zones in an airport have different lux requirements. For instance, check-in counters and customs desks are often lit to around 500 lux so staff can clearly read passports and documents. Waiting areas and lounges might aim for roughly 300 lux, providing a bright but relaxed environment for passengers. Circulation areas like corridors between gates, or baggage claim halls, might be maintained at around 150–200 lux as a general illumination level. These levels ensure that signage is readable and tasks like baggage handling are safely lit.
Airports are excellent candidates for daylight integration due to their high ceilings and large roof spans. Many modern airports feature dramatic skylights or even entire roofs made of translucent materials. Daylighting not only cuts energy usage in these typically 24/7 facilities, but also adds to the architectural appeal – daylight makes spaces feel larger and more pleasant, improving the passenger experience. Skylights in airports can range from narrow linear strips along the ceiling to grand vaulted canopies over a central atrium. Polycarbonate skylight systems are particularly favored in some airport designs because they are lightweight (important for large-span structures) and extremely impact resistant (able to withstand hail or debris, which is a consideration for wide roof areas). For example, a polycarbonate barrel vault skylight stretching over a terminal concourse can shower the interior with natural light, easily achieving a few hundred lux under daylight conditions. This can complement artificial lighting to meet the required 300 lux in waiting areas while giving travelers a view of the sky. Fiberglass (GRP) skylights can also be used, often in modular panel form, to diffuse sunlight in areas where a softer light is preferred (to avoid glare on glossy floors or screens). A real-world scenario is using diffusing GRP skylight panels over security screening areas, providing ample light without the glare that could impede CCTV cameras or the comfort of people looking upward. DOMER’s ContiRoof polycarbonate systems and Vivid GRP panels can both be adapted for such large-scale applications, ensuring that an airport’s design goals and illumination needs are met. The materials are engineered with high UV protection and fire safety ratings, which are crucial in public facilities. By using skylights, airports can maintain those 150–500 lux recommendations in a more sustainable way, reducing the burden on their electrical systems and creating a travel environment that feels open and naturally lit.
Polycarbonate vs. Fiberglass (GRP) Skylights: Key Technical Differences
When specifying a skylight or translucent roofing system, the choice of material – polycarbonate or fiberglass (GRP), influences performance attributes like light quality, durability, and maintenance. Both materials are used in commercial skylights, but they have distinct characteristics. Below are the key technical differences and considerations:
- Light Transmission and Diffusion: Polycarbonate glazing is highly transparent and can offer very high visible light transmission (often 85% or more, depending on thickness and coatings). This means a clear polycarbonate skylight will let in a large portion of the sunlight, producing bright light and even direct sun patches inside. GRP skylights (made of translucent glass-fiber reinforced polyester) usually have a diffused translucency, they scatter incoming light. While their overall transmission might be slightly lower than clear polycarbonate, quality GRP panels still provide substantial daylight (commonly in the range of 75% transmission) but with a soft, diffused glow. The diffused light from GRP is excellent for eliminating harsh shadows and hotspots. For example, Domer Vivid GRP panels are designed to render daylight uniformly so that interior lighting is balanced with no glaring zones. Polycarbonate skylights can also be made to diffuse light (using frosted or prismatic surfaces) if a project requires it, but standard polycarbonate tends to be clearer. The choice often comes down to whether you want a crystal-clear skylight (polycarbonate) or a naturally diffusing skylight (GRP) for your application.
- Strength and Impact Resistance: Both polycarbonate and GRP are significantly tougher than traditional glass, but polycarbonate is in a class of its own for impact strength. Polycarbonate panels are up to 200 times stronger than glass, meaning they can withstand heavy impacts (like hailstorms, wind-borne debris, or even accidental foot traffic on the roof) without cracking. This makes polycarbonate ideal for areas with extreme weather or where skylights must be non-fragile. GRP skylights are also quite durable, the glass fibers provide good tensile and flexural strength to the panels. In fact, high-quality GRP skylights can be engineered to be non-fragile as well, capable of sustaining an accidental footfall without breaking. However, GRP’s impact resistance is generally lower than that of polycarbonate; a very hard blow that might dent a polycarbonate sheet could potentially crack a fiberglass panel. Manufacturers like DOMER mitigate this by using superior resin formulations and fiber layouts – e.g., a Domer Vivid panel of 1.5 mm thickness has a tensile strength of over 135 MPa, versus ~80 MPa in some standard GRP sheets. In summary, both materials are strong enough for most climates, but polycarbonate offers a higher margin of impact safety, which is why it’s often used in facilities expecting hail or in vulnerable roof positions.
- UV Resistance and Weathering: Exposure to ultraviolet (UV) rays can degrade many plastics over time, causing yellowing, loss of clarity, and embrittlement. Both polycarbonate and GRP skylights need protection against UV to ensure longevity. High-quality polycarbonate skylights come with co-extruded UV protective layers on the exposed surface, blocking the majority (often 99%) of harmful UV radiation. This preserves the clarity of the sheet and protects interiors (and occupants) from UV. GRP skylights similarly can be made with special gel coats or surface films that incorporate UV inhibitors. For instance, Domer’s GRP skylights use a “UV Premium Shield” surface, and an even more robust “UV Platinum Shield” option, to virtually eliminate UV transmission and prevent the typical discoloration seen in older fiberglass panels. With these protections, DOMER reports that their GRP skylights can maintain performance for up to 20 years without yellowing. In terms of visible aging, polycarbonate without UV coating would yellow noticeably within a few years of harsh sun exposure, and basic fiberglass would turn brittle and darken as well. Therefore, it’s crucial that whichever material is chosen, it comes from a manufacturer that provides proper UV stabilization. When UV protection is in place, both materials will weather well, retaining their light transmission for many years. Regular inspections are still wise, but maintenance related to UV aging is minimal for coated polycarbonate and quality GRP.
- Thermal Insulation and Energy Efficiency: A skylight isn’t just about light, it’s also part of the building envelope, which means its thermal properties matter. In general, multi-wall or multi-layer polycarbonate skylights and multi-skin GRP panels can offer good insulation values, helping to maintain indoor temperatures. Polycarbonate skylights are often available in twin-wall or multi-wall configurations (with air gaps), greatly improving their U-value (lower U-value = better insulator). GRP skylights can be built as double or triple-skinned units as well, or installed as sealed factory-assembled panels with insulating layers (like DOMER’s Vivid TP which is an insulated GRP skylight panel). Such designs ensure that while light comes in, heat transfer is reduced, keeping the building cooler in summer and warmer in winter. Polycarbonate by itself has a lower thermal conductivity than glass, so even a solid polycarbonate sheet insulates better than a single pane of glass. But for most commercial projects, one would use the engineered systems: for example, a standing-seam polycarbonate skylight system might have a U-factor comparable to a double-glazed window, due to the air gap and thermal breaks. GRP panels also naturally diffuse solar energy; they can have a favorable solar heat gain coefficient (SHGC) if they are slightly tinted or pigmented, meaning they admit lots of visible light but filter some infrared heat. Some advanced polycarbonate systems incorporate infrared-reflective coatings or tints that allow daylight but reflect IR, further reducing heat gain. In summary, both materials can contribute to an energy-efficient building by reducing lighting loads and managing heat. The exact performance will depend on the product configuration (single vs multi-layer, any low-E coatings, etc.). It’s worth noting that building codes in many regions mandate certain insulation values for skylights, DOMER’s skylight systems are designed to meet or exceed these standards by offering superior heat insulation while still maximizing light transmission.
- Maintenance and Longevity: From a maintenance standpoint, polycarbonate and GRP skylights are relatively low-maintenance, especially when compared to glass which might require frequent cleaning to maintain clarity. Polycarbonate has a hard, smooth surface that generally does not accumulate dirt easily; many come with surface treatments that resist abrasion and repel dust (e.g., DOMER’s Durapoll AR, an abrasion resistant polycarbonate sheet, is one such example). Occasional cleaning with water and a mild detergent is usually enough to keep polycarbonate skylights clear. GRP skylights can have a slightly textured surface due to the embedded fibers, but high-quality ones are usually finished with a smooth top layer (gelcoat or film) that similarly helps in shedding dirt. Over decades, a poorly made fiberglass panel might experience fiber bloom (where fibers become exposed on the surface), this can trap dirt and degrade light quality. However, with modern manufacturing, this is mitigated. For instance, DOMER’s GRP skylights with the UV shields maintain their smooth, glossy surface for the long term, avoiding major dirt accumulation or yellowing. Polycarbonate panels can last decades, often the warranty for polycarbonate skylights is around 10 years, but actual lifespan can be well beyond that if not mechanically damaged. It’s important to periodically inspect seals, fasteners, and flashings for any wear, since leaks are more likely to develop from flashing failure than from the panel material itself. Both materials are thermoplastic/thermoset, so they don’t rust, and they handle moisture well. In summary, maintenance is straightforward, mostly keeping them clean and ensuring seals remain weather-tight. Both types offer long-term durability, but again, the product quality determines exact performance. This is why working with established brands like DOMER, who engineer skylights specifically for longevity (with high-strength resins, UV blockers, and proper sealing systems), is key to a successful daylighting installation.
DOMER Skylight Solutions for Maximum Light Transmission
As a leading manufacturer of daylighting systems, DOMER offers specialized sub-brands of polycarbonate and GRP skylights tailored for various commercial and industrial applications. These products exemplify how advanced design and material engineering can achieve optimal light transmission along with durability:
- DOMER’s Vivid Series (GRP Skylights): The Vivid line includes translucent GRP skylight panels such as Vivid PS (profile-matching corrugated skylights) and Vivid TP (insulated multi-skin panels). These skylights are built from premium glass-reinforced polyester, delivering high natural light throughput with a diffusing effect. A key feature of Vivid skylights is their ability to spread light evenly; even under direct sun, they create a soft daylight inside without glare. This makes them ideal for facilities like warehouses, factories, and sports halls where uniform illumination is desired. Vivid panels are engineered to integrate seamlessly with metal roofing profiles, maintaining weather-tightness. They come with DOMER’s “UV Premium Shield” or optional “UV Platinum Shield” coatings to ensure longevity (up to 25-year performance). They also achieve top-tier fire safety ratings (Class A per ASTM E84, etc.), meaning they meet stringent building code requirements for flame spread. The mechanical strength of these panels allows them to span large roof purlin distances and achieve non-fragility for safe roof access. In practice, specifying a Domer Vivid skylight in a logistic warehouse or a manufacturing plant means the building will have reliable, diffused daylight for decades, with minimal maintenance and strong resistance to environmental wear.
- DOMER’s Conti Series (Polycarbonate Skylights): Under the Conti brand, DOMER provides polycarbonate skylight systems like ContiRoof UL (a standing-seam continuous rooflight system), ContiVault SSCV (self-supporting curved vault skylight), and SkyDome (thermoformed dome skylights for localized lighting). These systems leverage the strengths of polycarbonate, high clarity, toughness, and light weight. For example, ContiRoof UL is a standing seam panel system that can form long, continuous rows of skylights on a roof without the need for metal framing between panels. This system offers an airtight, waterproof seal and excellent thermal insulation, thanks to its multi-wall polycarbonate construction and interlocking design. It’s well-suited for commercial and industrial buildings where you want maximal light with no leaks. ContiVault, on the other hand, creates arching roof windows (barrel vaults) out of polycarbonate, ideal for large open spaces like stadiums, atriums, or big factories – the arch shape further enhances load capacity and allows light to enter from various angles. All these polycarbonate solutions come with built-in UV protection, blocking 99% of harmful UV rays so that neither the panels nor the occupants are exposed to UV. DOMER’s polycarbonate skylights are also available with solar control features that reflect infrared heat while admitting visible light, which is extremely valuable in hot climates or temperature-controlled buildings. The result is a bright space without the greenhouse effect. Installing a Conti series skylight system means getting a high-transmission daylighting solution that is also engineered for fast installation (the standing seam panels, for instance, click together without through-fasteners, simplifying construction). These systems have been used globally in projects ranging from logistic park warehouses to airport terminals, proving their versatility.
- DOMER Lumina Tubular Skylights: In addition to broad-area skylights, DOMER’s portfolio includes tubular daylighting devices (the Lumina series) which are essentially high-performance light tubes. These are useful for getting daylight into smaller or lower-level spaces in commercial buildings. A rooftop dome captures sunlight, channels it down a highly reflective tube, and diffuses it through a ceiling diffuser into the interior space. Lumina Tubular Skylights can deliver surprising amounts of light, often hundreds of lux in a focused area, ideal for offices, corridors, or specific task areas that are far from roof or window access. They are often used in retrofits where a full skylight is not feasible between existing roof structures. By including such options, DOMER ensures that architects and builders have a complete toolbox of daylighting solutions, whether the project is a sprawling factory roof or a small interior room that needs light.
In all of its skylight systems, DOMER emphasizes a tailored approach: understanding the project’s light level targets (lux requirements), climate conditions, and structural needs. This means a DOMER solution for a high-humidity coastal environment will factor in salt corrosion resistance and diffused light for overcast conditions, whereas a project in a desert climate will prioritize heat-reflective skylights and extra UV shielding. The ability to customize materials (like choosing between polycarbonate or GRP, selecting clear vs diffused finishes, or adding insulation) allows building professionals to meet specific lux goals efficiently. For example, if an airport concourse needs 300 lux daylight and must also meet certain aesthetic design, DOMER could provide a ContiVault polycarbonate skylight with a slight tint to achieve that target without glare. Alternatively, if a factory needs 200 lux on the floor with no direct sun on workers, a double-skin Vivid GRP skylight system could be supplied to give exactly that diffused illumination. By featuring these DOMER products and sub-brands, we illustrate how modern commercial skylight systems are at the intersection of material science and practical design, delivering bright natural light, structural reliability, and energy savings all in one package.
Conclusion
Achieving optimal light transmission in commercial and industrial buildings is a multifaceted challenge – it requires meeting the recommended lux levels for various tasks while keeping energy usage and comfort in mind. Skylights made from polycarbonate and fiberglass (GRP) have proven to be indispensable tools in this regard. They bring abundant natural daylight into large structures like warehouses, logistic parks, shopping centers, factories, offices, and airports, helping to reach the lux levels needed for safety and productivity. At the same time, they reduce reliance on artificial lighting during the day, which can lead to significant energy savings and a lower carbon footprint for the building.
We’ve seen that different facilities have different lighting needs, from a modest 150 lux in a storage bay to a bright 750 lux in a supermarket. Skylight systems can be configured to meet these needs by varying their area, distribution, and material properties. Polycarbonate skylights, with their crystal-clear high transmission and extreme toughness, are ideal for applications requiring maximum light and impact resistance (e.g., skylights in a hail-prone logistic warehouse, or a long span roof over a mall). GRP skylights, offering beautifully diffused light and excellent integration into roofing systems, are perfect when uniformity and thermal blending are paramount (e.g., in a manufacturing plant or an airport security hall).
Technically, both material options have advanced to a point where issues of the past, UV degradation, leakage, poor insulation, have been addressed through innovation. As we highlighted, brands like DOMER have set the bar high by introducing multi-layer panels, UV-blocking tech, and robust framing systems that ensure skylights perform reliably for decades. These products underscore the fact that modern skylights are industrial daylighting solutions in the truest sense: they are engineered products contributing to a building’s overall performance.For architects and building contractors looking to specify daylighting, the key takeaways would be: assess the lux requirements of each space, consider the benefits of natural light for those needs, and choose a skylight system (polycarbonate, GRP, or a hybrid) that best aligns with those goals. Always opt for high-quality, proven systems, like DOMER’s polycarbonate and fiberglass skylights – which offer the necessary light transmission along with durability, UV resistance, and energy efficiency. With the right design and product, skylights will not only meet the lux targets but will exceed expectations in enhancing the space’s ambiance and sustainability. In conclusion, leveraging skylights is a brilliant way to “let the sky in” illuminating large buildings with nature’s light, for optimal performance and comfort inside.