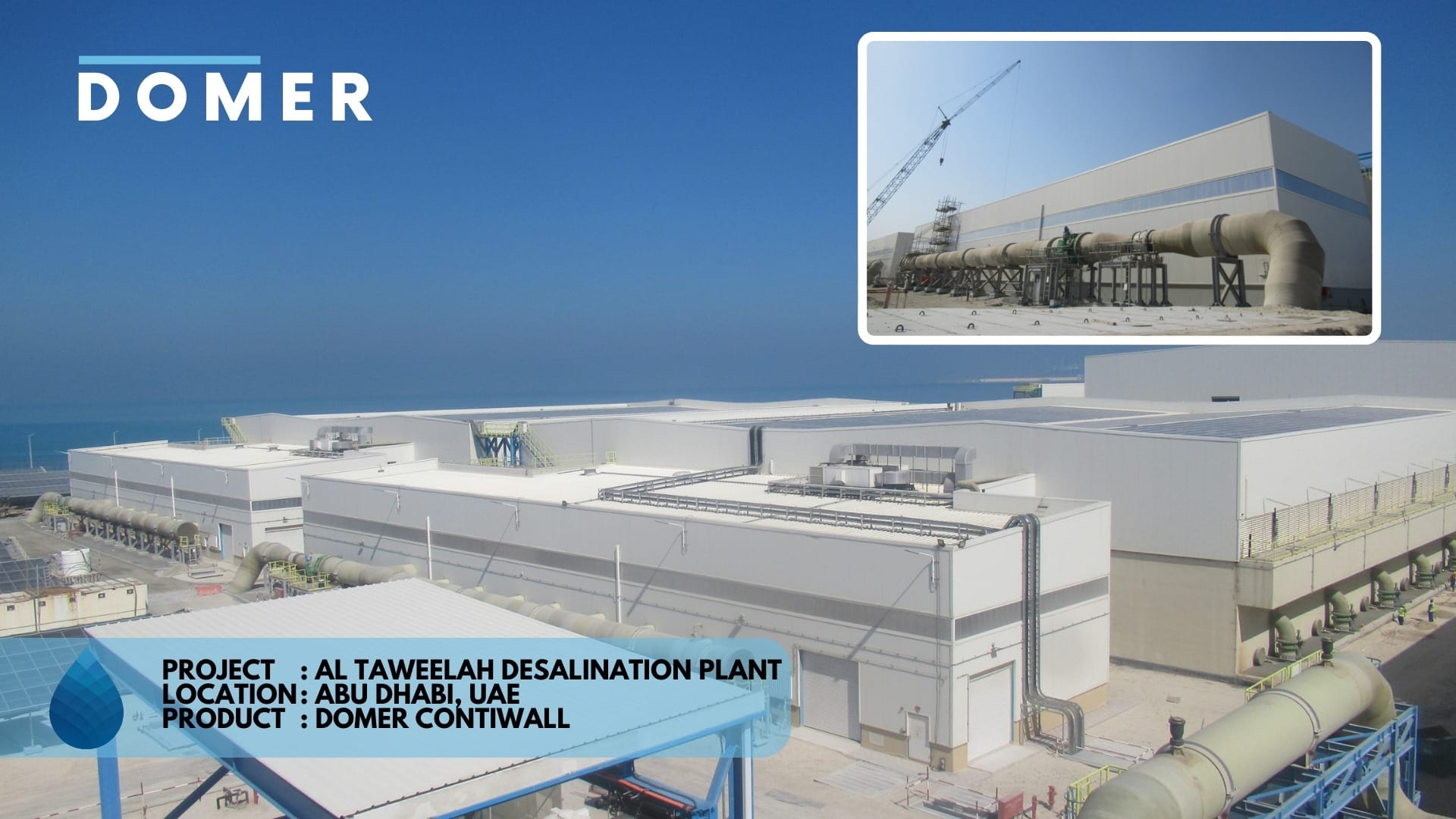
Introduction
The Al Taweelah Desalination Plant in Abu Dhabi – slated to be the world’s largest reverse-osmosis (RO) water desalination facility at 909,200 m³ per day capacity, demanded building materials that could meet extreme performance criteria. Initially, conventional double-glazed glass was chosen for its façade and skylights, but a transition to an advanced polycarbonate facade solution was soon implemented. DOMER ContiWall CL40, a state-of-the-art 40 mm polycarbonate panel system, replaced traditional designed glass and delivered superior insulation, durability, and daylighting. This report details how the switch from double glazing to DOMER’s ContiWall CL40 system provided numerous advantages, from an exceptional U-value of just 1 W/m²K to 250× the impact resistance of glass, while ensuring the structure remains 100% waterproof and dustproof in harsh industrial conditions.
From Double-Glazing to DOMER ContiWall CL40
Switching from conventional double-glazed glass to a DOMER ContiWall CL40 polycarbonate facade was a strategic decision driven by performance and longevity. Double-glazing, though common for thermal insulation, is heavy and fragile in an industrial setting. Glass panels require substantial framing and are prone to shattering upon impact or under high stress. Even insulated glass units typically have higher thermal conductivity (poorer U-values) and can suffer seal failures over time, leading to leaks or fogging. In contrast, the DOMER ContiWall CL40 system offered a lightweight yet ultra-strong alternative. Polycarbonate is up to 250 times stronger than glass, giving it unparalleled impact resistance against shocks, hail, or debris. This strength meant the desalination plant’s cladding could withstand the vibrations and occasional impacts in a heavy industrial environment without risk of cracks or hazardous shattering. Additionally, at just a fraction of the weight of glass, the ContiWall panels put far less load on the building structure, allowing for simpler support framing and easier installation. By moving to ContiWall CL40, the Al Taweelah facility gained a facade that is not only more durable but also more thermally efficient and maintenance-friendly than the previous glass solution.
Advantages of DOMER ContiWall CL40 Polycarbonate Facade
The DOMER ContiWall CL40 system brought a host of performance benefits to the project. Key advantages of polycarbonate over traditional glass in this application include:
- Superior Thermal Insulation: With a U-value of 1.0 W/m²K, ContiWall CL40 dramatically reduces heat transfer. Its multi-wall polycarbonate construction traps air layers, providing “extreme thermal insulation” that surpasses most double-glazed glass units in energy efficiency. This helps maintain stable indoor temperatures and lowers HVAC energy usage at the plant. In the UAE’s climate, such insulation is critical to keep facilities cool without excessive cooling costs.
- Exceptional Light Diffusion & Daylighting: Unlike clear glass, ContiWall’s polycarbonate panels have an internal multi-diamond structure that diffuses incoming sunlight. They transmit abundant natural light while eliminating glare and hotspots. In effect, the translucent walls act as giant polycarbonate wall lights, flooding interior spaces with soft, even daylight. This “healthy natural light transmission” improves visibility for workers and reduces the need for artificial lighting. By day, the façade provides bright ambient light, and by night it can give a pleasant glow when interior lights are on – turning the building into a beacon without the harshness of transparent glass.
- UV and IR Protection: ContiWall CL40 panels come with a co-extruded UV-protective layer that blocks harmful ultraviolet rays, preventing interior sun damage and yellowing of the panels over time. They also filter out a significant portion of infrared radiation, cutting down solar heat gain. This IR protection means less heat buildup indoors, contributing to cooler interior conditions. In a desert environment, the combination of UV shielding and IR heat reduction enhances comfort and protects equipment, all while allowing visible light to pass through.
- Extreme Impact Resistance: Polycarbonate’s toughness is legendary, over 200–250× the impact resistance of glass. The ContiWall CL40 facade can absorb impacts (from wind-blown debris, mechanical shocks, or accidental collisions) that would shatter conventional glass. This dramatically improves safety and longevity. The multi-wall panel design adds even more rigidity and strength. For a heavy industrial plant, this resilience means fewer repairs and no costly downtime due to broken windows or panels. It also enhances security, as the panels are virtually unbreakable under manual impact, unlike brittle glass.
- Lightweight Construction: Despite its strength, the polycarbonate system is remarkably lightweight, far lighter than an equivalent glass assembly. Each 40 mm ContiWall panel weighs only a fraction of a comparable double-glazed glass panel, easing handling and installation. The lightweight panels enabled faster installation at Al Taweelah with smaller cranes and crews, and they imposed less structural load on the building. This is particularly valuable for large-scale projects where material weight can significantly impact the design and cost of support steelwork.
- 100% Waterproof and Dustproof Performance: DOMER’s ContiWall CL40 features a unique tongue-and-groove locking system that creates a continuous weather-tight seal between panels. Thanks to precision extrusion, each panel snaps perfectly into the next, achieving full air and water tightness across the facade. This means the cladding is inherently waterproof, no rain or spray can penetrate, and completely dustproof to combat the frequent sandstorms and dust in the region. Unlike conventional glazing that relies on sealants or gaskets (which can degrade) at joints, the ContiWall system’s integrated joints ensure long-term leak-free performance. The result is a maintenance-free envelope that keeps the plant’s interior and sensitive equipment protected from water ingress, salt spray, and fine dust.
- Fire Safety Compliance: DOMER ContiWall CL40 is engineered with fire-retardant polycarbonate material and profiles that meet stringent European fire standards. It has been certified to EN 13501-1 with a Class B s1 d0 rating, indicating very limited flame spread, the lowest smoke production (s1), and zero flaming droplets (d0) in a fire situation. This compliance provides a high level of safety for an industrial facility, ensuring that the facade will not significantly contribute to a fire and will not produce heavy smoke or flaming debris. Achieving Class B-s1,d0 is a remarkable feat for a thermoplastic material, underscoring the advanced fire-resistant formulation of the ContiWall panels.
Each of these advantages played a crucial role in the success of the Al Taweelah project. Below, we explore in more detail two standout features of the ContiWall CL40 system – its innovative sealing mechanism and its performance in an industrial context, as well as DOMER’s manufacturing excellence that makes such performance possible.
Innovative Tongue-and-Groove Locking System Ensures Airtight Sealing
One of the most innovative aspects of the DOMER ContiWall CL40 design is its tongue-and-groove interlocking panel system. Each polycarbonate panel is extruded with a male “tongue” on one edge and a female “groove” on the opposite edge. During installation, panels slide and snap together along these edges with high precision, resulting in a seamless facade without gaps. This engineering eliminates the typical gaps or silicone joints between panels seen in traditional glazing systems. The high-precision extrusion of the panels means the fit is extremely tight, creating a continuous compression seal that is naturally waterproof and airtight once the panels are locked.
Because of this self-sealing mechanism, the ContiWall system does not rely solely on perimeter framing for weather-proofing. Even at the joints between panels (mid-span on the facade), the connection is secure against water ingress. This contrasts with conventional glass curtain walls, where metal mullions and rubber gaskets or sealant are required at every joint to prevent leaks. In the harsh coastal desert environment at Al Taweelah, this feature proved invaluable, wind-driven rain, saline humidity, and fine dust are all kept out without the need for heavy seal maintenance. The tongue-and-groove joints maintain their integrity over time, as the polycarbonate’s slight flexibility accommodates thermal expansion and vibration, whereas rigid glass and sealant joints might crack or lose adhesion. The result is a facade that remains fully weather-tight and low-maintenance throughout its lifespan. Additionally, the interlocking panels provide robust structural stability; the “plug-in seamless system” effectively makes the array of panels behave like a single continuous wall, capable of withstanding pressure differentials and impacts collectively. Overall, the ContiWall CL40’s clever locking system is a triumph of design, ensuring zero leaks and zero dust ingress even in the demanding conditions of a desalination plant.
European-Class Fire Safety for Industrial Peace of Mind
Safety is paramount in any construction, especially in industrial facilities. While polycarbonate is a combustible material, DOMER has formulated the ContiWall CL40 system to achieve a Class B-s1,d0 fire rating under EN 13501-1 standards. In practical terms, this means the panels exhibit very limited contribution to a fire (Class B), produce little to no smoke (s1), and do not form flaming droplets/particles when exposed to fire (d0). This level of fire performance is on par with or better than many flame-retardant building materials used in industrial construction. It ensures that in the unlikely event of a fire at the desalination plant, the polycarbonate facade will not ignite easily or spread flames rapidly, allowing more time for fire response and not adding to the smoke hazard for personnel.
Achieving B-s1,d0 is a significant quality mark for DOMER’s product, as many standard polycarbonate sheets would typically achieve lower ratings without special additives. The ContiWall panels likely incorporate flame retardant additives and a careful design of the polycarbonate cells to self-extinguish. Additionally, the thermally broken aluminum framing used to secure the panels is made of non-combustible metal, which helps in containing any fire. For the Al Taweelah project, compliance with European fire safety standards provided confidence to stakeholders that the new polycarbonate facade meets rigorous safety benchmarks. It demonstrates that industrial projects need not compromise on fire safety even when adopting modern materials. DOMER’s commitment to safety is evident in its testing and certification of ContiWall CL40 for use in large-scale buildings where fire code compliance is non-negotiable.
From Modern Architecture to Heavy Industry: Versatility of ContiWall CL40
Polycarbonate facade systems like ContiWall CL40 are often associated with modern architectural designs – glowing building envelopes, translucent office block facades, and innovative skylights. Indeed, DOMER ContiWall has been used to create striking illuminated facades for contemporary projects in Abu Dhabi. However, the Al Taweelah Desalination Plant case underscores that ContiWall is equally suited for heavy industrial applications. This versatility is a testament to the material’s robust performance and DOMER’s engineering expertise.
In an industrial setting such as a desalination plant, there are unique challenges: high humidity and salt exposure, constant equipment vibration, potential mechanical impacts, and the need for easy maintenance. The ContiWall CL40 system rose to these challenges in multiple ways. First, its industrial-grade durability means it can shrug off the bumps and knocks that are inevitable in a busy plant (far better than glass, which would crack under similar abuse). Second, the sealed dustproof design is crucial – desalination plants have large pumps and motors that must be kept free of dust and sand ingress. By using a facade that is inherently dust-tight, the facility protects its internal environment and reduces filtration burdens on HVAC systems. Third, the thermal efficiency of the panels helps stabilize the internal climate. Even in an industrial plant, controlling the indoor temperature is important for both equipment and personnel. The superior insulation of the polycarbonate walls keeps the scorching desert heat at bay better than the old glass walls did, thereby improving energy efficiency and working conditions. This reflects the general advantage of polycarbonate in industrial buildings such as warehouses or factories – it significantly lowers heat transfer, reducing cooling loads.
Another advantage in the industrial context is ease of installation and replacement. Large industrial projects value solutions that can be installed quickly to meet tight construction schedules. The ContiWall’s lightweight modular panels and simple locking mechanism allowed the installation team at Al Taweelah to clad a huge area rapidly, saving on labor and downtime. In the future, if a panel ever needs replacing (due to extraordinary damage, for example), it can be swapped out without dismantling an entire curtain wall module – the tongue-and-groove panels can be individually removed and replaced fairly easily, unlike giant glass panes. This modular replaceability is a big plus for maintenance in remote industrial sites.
It’s important to note that none of these industrial benefits come at the expense of design. The Al Taweelah plant’s architecture gained an aesthetic boost from the ContiWall system – during the day the facades are a sleek translucent white, and at night they emit a subtle glow when interior lights are on, embodying an architectural wall-light effect. For a utilitarian facility, this elevates its appearance to something more iconic, all while remaining functional. DOMER’s ContiWall CL40 thus proves that a product can be both architecturally appealing and industrially pragmatic. Its use ranges from avant-garde city buildings to infrastructure projects, bridging the gap between modern design trends and hardcore industrial requirements.
DOMER’s Manufacturing Excellence and R&D Leadership
Delivering a product like ContiWall CL40 requires cutting-edge manufacturing and a commitment to quality. DOMER’s manufacturing excellence underpins the performance of each panel installed at Al Taweelah. The polycarbonate panels are produced using advanced co-extrusion technology under tightly controlled conditions. This ensures that the multi-wall (multi-diamond) internal structure is formed perfectly in every panel, giving consistent strength and insulation performance. High-precision extrusion also guarantees the tongue-and-groove profiles on each panel align exactly, which is critical for the system’s waterproof sealing to work. DOMER employs strict quality control at its production facilities – each batch of panels likely undergoes dimensional checks, optical quality inspection, and impact testing to make sure it meets the specified standards. By maintaining such rigorous QC, DOMER can confidently supply thousands of square meters of ContiWall panels, knowing they will perform uniformly across an entire façade.
Research and development (R&D) is another pillar of DOMER’s leadership in polycarbonate facade technology. The company continuously innovates in material formulation and panel design. For instance, developing a polycarbonate panel that achieves a B-s1,d0 fire rating requires substantial R&D to fine-tune flame retardant additives without compromising clarity or strength. DOMER’s R&D efforts have also led to enhancements in UV coatings, ensuring the ContiWall panels have long-term resistance to UV yellowing despite the intense Middle Eastern sun. The multi-diamond cell structure inside the CL40 panel is a result of design optimization, it provides superior stability and insulation, which came from iterative engineering and testing. Additionally, DOMER’s investment in extrusion technology allows them to produce panels of unlimited length and customized colors to suit different project needs (as hinted by their product features). This manufacturing flexibility is crucial for tailoring solutions to specific architectures, whether it’s a continuous 11-meter-long wall panel for a factory or a special tinted skylight for an airport.
Furthermore, DOMER’s technical team works closely with architects and engineers (a custom-engineered approach), demonstrating a commitment to application-driven R&D. They adapt their systems to meet regional requirements from thermal performance to fire codes, and this was evident in the Al Taweelah project where ContiWall CL40 was customized to excel under local climate conditions. Such a focus on innovation and quality ensures DOMER remains at the forefront of polycarbonate facade technology. Clients in both the architectural and industrial sectors can trust that DOMER’s polycarbonate solutions are backed by deep expertise and uncompromising manufacturing standards.
Conclusion
The application of DOMER ContiWall CL40 at the Al Taweelah Desalination Plant showcases a successful integration of advanced material technology in a demanding industrial project. By replacing conventional double-glazing with a polycarbonate facade system, the project reaped multiple benefits from thermal efficiency and diffused daylight to rugged durability and weather-tight performance. The ContiWall CL40 panels provided the plant with a facade that is cooler, brighter, safer, and stronger, all while being easier to install and maintain. Crucially, these improvements did not require sacrificing aesthetics or safety; the system meets top-tier fire standards and adds visual appeal to the facility.This case underlines the advantages of polycarbonate in modern construction: a well-designed polycarbonate facade can outperform glass in key areas like insulation and impact resistance, making it a compelling choice not only for sleek commercial buildings but also for heavy-duty industrial complexes. DOMER’s ContiWall CL40 exemplifies how innovation in materials and manufacturing can solve real-world challenges – delivering a facade solution that thrives in extreme environments. As a result, the Al Taweelah Desalination Plant stands as a forward-thinking project, leveraging DOMER’s polycarbonate facade expertise to ensure long-term operational excellence. In summary, the partnership between cutting-edge material (ContiWall CL40) and a critical infrastructure project has proven to be a winning combination, setting a precedent for future industrial facilities to adopt polycarbonate facade systems for their myriad benefits.
Ready to upgrade your project with DOMER ContiWall? Contact our experts today.